Copper Wire Recycling Machine for Sale
Continuous waste tyre pyrolysis plant is for processing waste tyres into fuel oil and carbon black for recycle use. It mainly includes waste tyre pretreatment system, continuous pyrolysis system with continuous feeding and discharge system controled by PLC system. The main part is the continuous pyrolysis system. Due to continuous feeding and discharge system, the continuous waste tyre pyrolysis plant can keep working without stop, thus to save energy and time. Also PLC control system makes much less labour cost.
- Email:
- Phone/WhatsApp/WeChat:
+86-135-2669-2320
- Video
- Raw Material
- Working Process
- Parameters
- Advantages
- Product Uses
- Cases
- Contact US
FEEDSTOCK
For our continuous waste tyre pyrolysis plant, the applicable raw materials can be any kinds of waste tyres, such as bicycle tyres, motorcycle tyres, car tyres, truck tyres, OTR tyres, and waste rubber, inner tube, waste rubber hose, waste rubber overshoes, etc.
WORKING PROCESS
To keep continuous feeding and discharge system, it requires the waste tyres should be in small size. So before continuous pyrolysis process, the waste tyres should be shredded into small pieces. As for detailed process, please check as below.
-
1.Collect waste tyres
All kinds of waste tyres are available, from small car tyres to big OTR tyres.
-
2.Shred tyres
Use a specialized tyre shredder to process big whole tyres into 3-5cm small pieces for easy feeding. The tyre shredder is a single and fully automatic shredding system, which can be directly connected to the feeding system of the continuous wasete tyre pyrolysis plant, which no need any transfer process.
-
3.Feeding
Through the unique sealed feed system, the broken tyre blocks are fed into the pyrolysis reactor for a sustainable feed process.
-
4.Heating & Continuous pyrolysis process
Heat the pyrolysis reactor by fuel oil, LPG, or natural gas. During the heating process, the pyrolysis reactor will rotate 360 degrees, so that the broken tyre blocks in the reactor will be uniformly heated. When the temperature rises to about 300℃, the tyres began to crack into oil gas.
-
5.Cooling
The oil gas will flow into the three-stage condensing system, where it is cooled by circulating cooling water into liquid oil. Then liquid oil is collected into the oil tank. The left is non-condensable gas which will be recycled to heat the reactor or collected for other heating.
-
6.Discharge
When oil gas is produced, carbon black will also be produced. It can be discharged through a carbon black slag discharge system, which is sealed and environmentally friendly. Moreover, we have designed related equipment that can directly press carbon black into carbon black balls and then sell them.
Technical data of continuous waste tyre pyrolysis plant
无法在这个位置找到: table1.htmUNIQUE ADVANTAGES OF DOING CONITNUOUS WASTE TYRE PYROLYSIS PLANT
- 1. Continuous working for 24 h/d: DOING conitnuous waste tyre pyrolysis plant can keep working for 24 hours a day. It employs an automatic feeding and discharging system, which can work at the same time. So you don’t have to wait for cooling down to discharge. Also, you can save time and fuel for pre-heating the reactor.
- 2. Fully automatic with low labour cost : DOING conitnuous waste tyre pyrolysis plant is controled by PLC system with automatic feeding and discharge system, which only need 2-3 worker to operate the PLC or computer, which makes it easy and efficient to operate to save labor force input.
- 3. Precise calculation system to ensure full pyrolysis and high oil yield: DOING continuous waste tyre pyrolysis plant is equipped with an accurate calculation system to ensure that the tyre is fully pyrolyzed in the reactor, and fully converted into oil gas, thus the oil yield is high.
- 4. Big capacity with small land occupy size: Also due to continuous feeding and discharge system, and unique reactor design, our fully automatic continuous waste tyre pyrolysis plant can process at least 10 tons waste tyres per day, up to 100T/D. And it takes up very little space, saving customers space costs and increasing profits.
- 5. Internal rotating for conitnuous operation: For external rotating system, you have to change the sealing material every three days, thus cannot achieve the real sense of continuous process. But our continuous waste tyre pyrolysis reactor adopts internal rotating method, which no need to worry about the sealing of the external rotating system.
- 6. Unique sealed feed and slag discharge system to ensure safety and environmental protection: The feed and slag discharge system of continuous waste tyre pyrolysis plant adopts unique seal design, which can effectively prevent pyrolysis oil gas from leaking through the feed inlet and slag discharge port, ensuring production safety and environmental protection.
Final products and their application
无法在这个位置找到: table2.htmPROJECT CASE
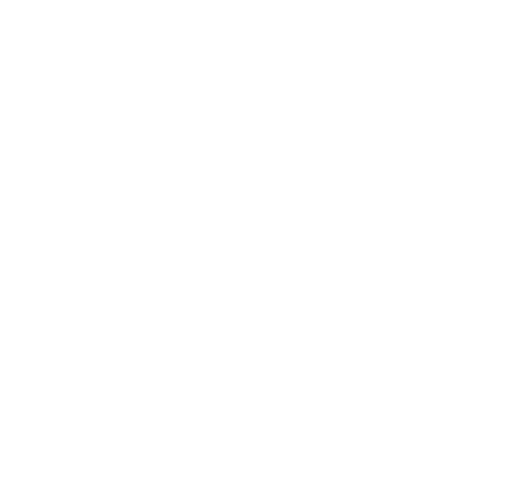