Product
Project Case
-
DOING 15TPD semi-continuous pyrolysis plant was installed in Brazil
-
1TPD Waste Oil to Diesel Refinery Machine Operation Site in Thailand
-
Transforming Paper Mill Plastic Waste into Diesel Plant Installed in Mexico
-
-
-
DOING Waste tyre to diesel recycling plants were successfully installed in Japan
-
Waste tire to diesel recycling plant was put into operation in South Africa
-
14MTPD Capacity of Waste oil recycling refinery plant project in Ghana
-
Continuous rubber tyre pyrolysis machine installed in Liaoning,China
-
50TPD fully continuous waste tyre pyrolysis plant installed in Russia
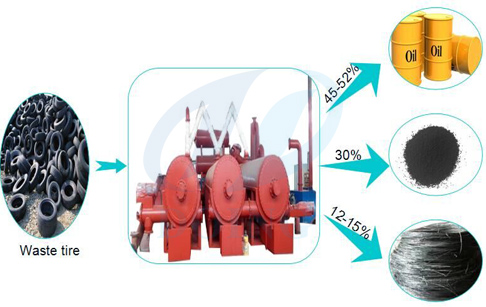
Fully automatic waste tyre to oil plant solutions
-
Cell/WhatsApp: +86-135-2669-2320
-
Phone: +86-371-56771821
-
E-mail: market@doingmachinery.com
Fully automatic waste tyre to oil plant includes waste tyre pretreatment system, continuous pyrolysis system with continuous feeding and discharge system controled by PLC system. The main part is the continuous pyrolysis system. Fully automatic waste tyre to oil plant is for processing waste tyres into fuel oil and carbon black for recycle use. Due to continuous feeding and discharge system, the fully automatic waste tyre to oil plant can keep working without stop, thus to save energy and time. Also PLC control system makes much less labour cost.
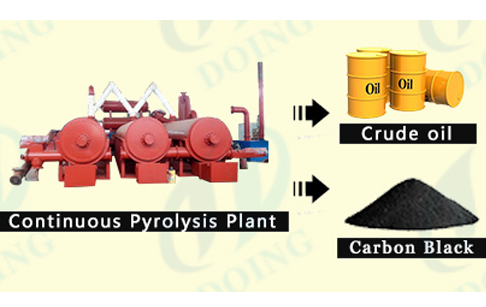
For our fully automatic waste tyre to oil plant, the applicable raw materials can be any kinds of waste tires, such as bicycle tires, motorcycle tires, car tires, truck tires, OTR tires, etc.
Excpet the steel wire extracted out from waste tires in the first stage pretreatment process, the final products from waste tire pyrolysis process will be fuel oil and carbon black.
To keep continuous feeding and discharge system, it requires the waste tires should be in small size. So before continuous pyrolysis process, the waste tires should be shredded into small pieces. And to avoid the steel wire mix with carbon black after pyrolysis process which is difficult to separate, it’s better to remove the steel wire from waste tires at first. As for detailed process, please check as below:
1. Collect waste tires: All kinds of waste tires are available, from small car tires to big OTR tires.
2. Remove steel wire: Use a steel wire pulling machine to pull out the steel wire from waste tires. The steel wire pulling machine is operated automatically, which only need one work for operation.
3. Shred tires: Use a specialized tire shredder to process big whole tires into 3-5cm small pieces for easy feeding. The tire shredder is a single and fully automatic shredding system, which can be directly connected to the feeding system of the continuous pyrolysis plant, which no need any transfer process.
4. Continuous pyrolysis process: Shredded tires go into the fully automatic waste tyre to oil plant, will firstly go through a mutiple pyrolysis reactor system to be pyrolyzed into oil gas. And oil gas will be cooling down to liquid oil through the cooling system. The residues (carbon black) will be pushed by continuous feeding tires to the carbon black dischrge system for discharge.
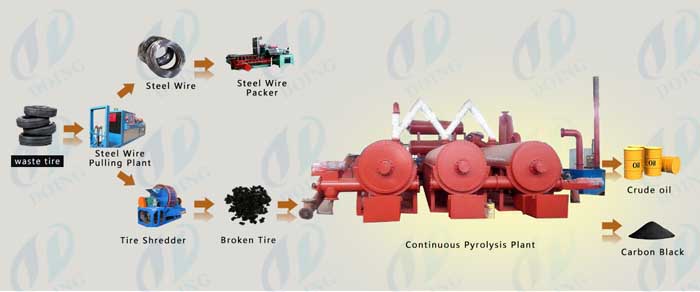
1.Fully automatic with low labour cost
Our fully automatic waste tyre to oil plant is controled by PLC system with automatic feeding and discharge system, which only need 1-2 worker for operating the PLC or computer is ok.
2.Fully pyrolysis for high oil output
Our fully automatic waste tyre to oil plant adopts mutiple reactor design which can make fully pyrolysis of waste tires, thus to get high oil output.
3.Big capacity
Also due to continuous feeding and discharge system, and unique mutiple reactor design, our fully automatic waste tyre to oil plant can process at least 10 tons waste tires per day, up to 100T/D.
4.Internal rotating for conitnuous operation
For external rotating system, you have to change the sealing material every three days, thus cannot achieve the real sense of continuous process. But our continuous waste tyre pyrolysis reactor adopts internal rotating method, which no need to worry about the sealing of the external rotating system.
5.Continuous working save time and energy
6.Long working life
During the continuous pyrolysis process, reactor heating is by indirect hot air heating, which will not damage reactor so much, thus to keep long usage life of the reactors. And since the hard steel wire already removed from waste tires before pyrolysis processs, thus no damage for the reactor.
Technical parameters of fully automatic waste tyre to oil plant
No. | Item | Specifications | ||||||
1 | Model | DY-C-10 | DY-C-20 | DY-C-30 | DY-C-50 | DY-C-60 | DY-C-80 | DY-C-100 |
2 | Cpacity | 10T/D | 20T/D | 30T/D | 50T/D | 60T/D | 80T/D | 100T/D |
3 | Power | 35Kw | 50Kw | 65Kw | 80Kw | 90Kw | 105Kw | 120Kw |
4 | Working type | Continuous | ||||||
5 | Reactor deisgn | Mutiple reactors (The quantity and size depends on the raw material condition) | ||||||
6 | Rotating | Internal rotating | ||||||
7 | Cooling system | Recycled waster cooling | ||||||
8 | Reactor material | Q245R/Q345R boiler plate | ||||||
9 | Heating method | Indireact hot air heating | ||||||
10 | Heating fuel | Fuel oil/gas | ||||||
11 | Feedstock | Waste tire/plastic/rubber | ||||||
12 | Output | Fuel oil, carbon black |
Solution of fully automatic waste tyre to oil plant
If you’re facing waste tires pollution or disposal problems, and be badly in need of a processing system, please feel free to contact us. We DOING Company are always ready to provide you the best solution.
Leave A Message
Please feel free to leave your contacts here and your privacy is protected. A competitive quotation will be provided according to your detailed requirement within one business day.
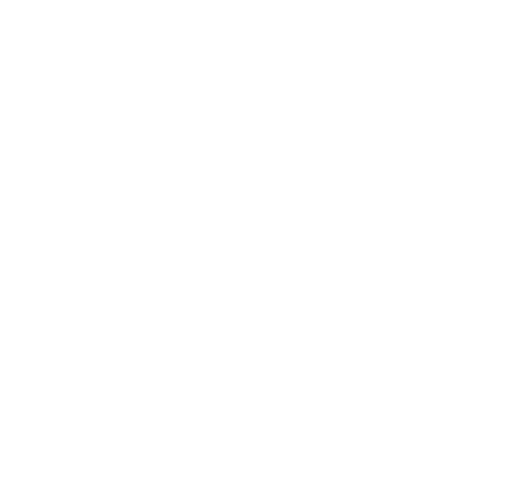