Contact Us
-
Cell/WhatsApp: +86-135-2669-2320
-
Phone: +86-371-56771821
-
E-mail: market@doingmachinery.com
FAQ
-
Continuous Pyrolysis plant
-
Oil Refining Machine
-
Auxiliary Equipment
Product
Project Case
-
DOING 15TPD semi-continuous pyrolysis plant was installed in Brazil
-
1TPD Waste Oil to Diesel Refinery Machine Operation Site in Thailand
-
Transforming Paper Mill Plastic Waste into Diesel Plant Installed in Mexico
-
-
-
DOING Waste tyre to diesel recycling plants were successfully installed in Japan
-
Waste tire to diesel recycling plant was put into operation in South Africa
-
14MTPD Capacity of Waste oil recycling refinery plant project in Ghana
-
Continuous rubber tyre pyrolysis machine installed in Liaoning,China
-
50TPD fully continuous waste tyre pyrolysis plant installed in Russia
How do we ensure the safety of our tire recycling machine in production?
2016-07-18 / Continuous Pyrolysis plant / Leave Message / Chat Online
1. What production standard we’re using for manufacturing the tire recycling machine?
As we know there is oil gas produced in pyrolysis process, so there may be pressure generated when wrong operation. To eliminate the safety risks, we make tire recycling machine strictly according to the standard of pressure vessel (boiler grade). The ellipsoidal head is an obvious symbol for pressure vessel. Because the reactor with ellipsoidal head has a strong tension and buffering when pressure generated. And it can better connect with the reactor body, therefore cannot be easily cracked under high pressure.
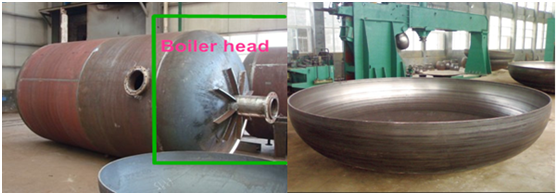
2. What kind of steel plate we’re using for making the tire recycling machine?
Since we’re making the boiler grade machine, of course we use boiler plate as raw material for the production. Through our experiences and the study, Q245R boiler plate is the best option for making tire recycling machine.
3. How thick is the steel plate we’re using for tire recycling machine production?
For tire pyrolysis machine, we need to heat it for pyrolysis tires to oil gas. If the plate is too thicker, the heat transfer will be greatly reduced, thus bring down the heating efficiency. Too thinner, it will be easy cracked after long term heated by high temperature. After years of experiences that 16mm plate is the best.
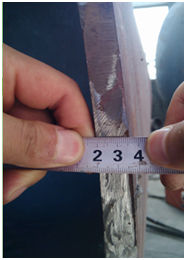
As we know that there are many suppliers in the market for providing this plate. How do we know the quality of their plate is good or not? So before production, we must make the raw material test to ensure it can meet our demand. Below are the testing devices for the steel plate in our lab.
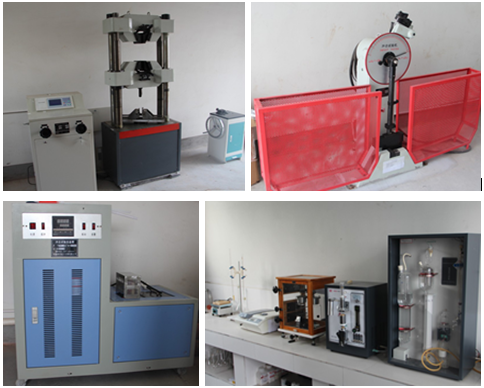
Technical equipment
To cut the steel pate accurately for better welding, we use plasma digital cutting machine which can be controlled by PLC. And after accurate cutting, the plate edge will be very neat for better welding. For welding, we use auto-welding machine, which can make the welding seam stronger than normal welding.
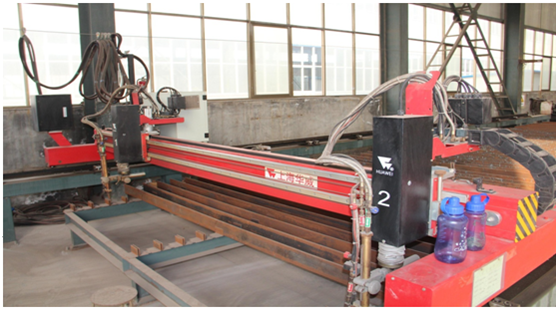
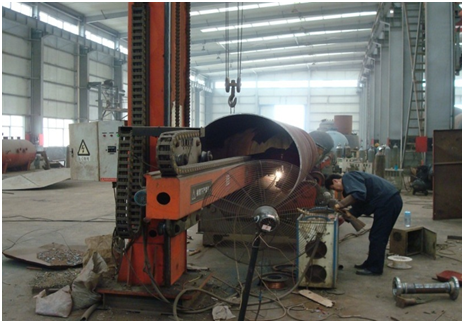
Auto-welding machine 02
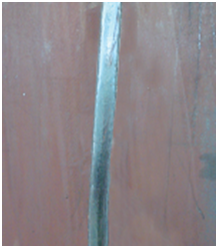
Welding details
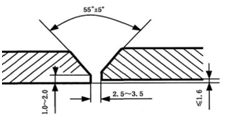
Drawing
6. How to ensure the welding seam is good enough?
After welding, we can see the welding appearance is very good. But how to know the welding seam is good or not. For us, we use X-ray detection for checking the welding seam after welding. We can see clearly if there are small pores inside the seam by X-ray detection. Even there is a very small pore, we’ll re-do it. By now we’re the first tire recycling machine manufacturer who has this technology. To operate the X-ray detection, the workers should get the operation licence.
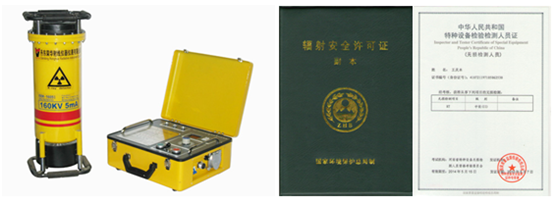
X-ray detecting for check
Leave A Message
Please feel free to leave your contacts here and your privacy is protected. A competitive quotation will be provided according to your detailed requirement within one business day.
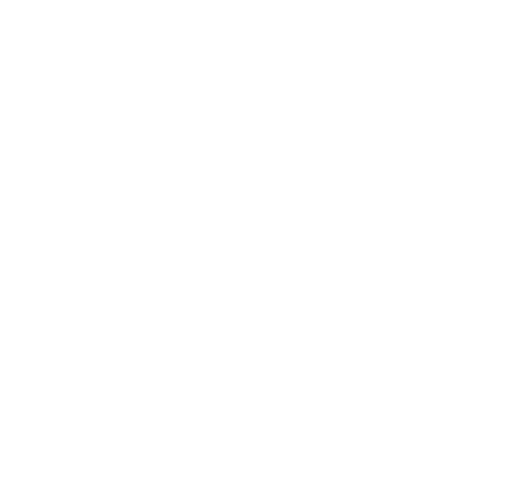