Philippines customer bought 10T
Contact Us
Waste plastic to diesel plant
The crude oil product that you obtain from the pyrolysis process can be used as furnace oil but it isn't sufficiently pur...

Skype:bonniezhao2

+86-135-2669-2320

+86-371-56771821

WhatsApp:0086 135 2669 2320
- Features:
- Technical Data:
- Application:
Among the many irremediable wounds that man is inflicting upon the environment, the improper disposal of waste plastic is growing into an alarming issue of concern.
Despite its amazing properties of strength, durability and its light weight, plastics have a major drawback: they can take up to 500-1000 years to naturally degrade. So if plastic had been discovered 500 years ago, and if Shakespeare used to brush his teeth, then his toothbrush would still be lying somewhere in someplace!
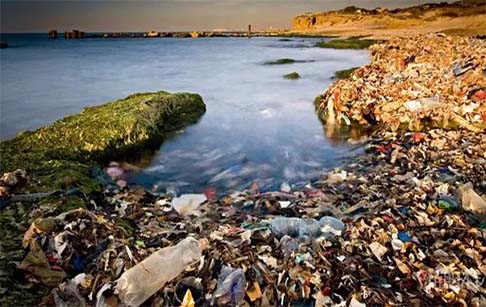
Waste oil
Some other issues with waste plastic are that it affects humans, animals and marine life; it causes soil infertility where dumped; and only 8% of all plastic waste is recycled! Sounds a trifle, right! Another lesser known factual reality is that for the production of plastic, 7% of the global crude oil is consumed, which is more than China's total crude oil consumption.
So what do we do with these ever-growing mounds of plastic waste? Bury plastic underground? Burn it? Or launch it into space! These solutions are more disastrous than the problem itself.
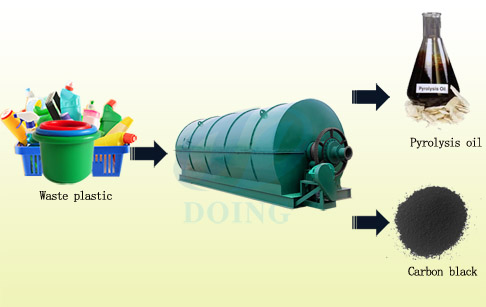
That’s why we developed the waste plastic pyrolysis plant process. This whole process include a pyrolysis process and a distillation process.
The basic pyrolysis process goes as follows:
1. Shredding or compressing for better feeding
Firstly, the waste material must be segregated and, if possible, be cleaned. Then it is shredded to speed up the reaction and to ensure that the reaction is complete.
2. Anaerobic heating
The shredded material must be heated in a controlled manner in an oxygen-free reactor. One of the most crucial factors in this operation is maintaining the right temperature(~430C for plastic) and the rate of heating, as they define the quality and the quantity of the final product.
3. Condensation
The gas that comes out from the reactor must be condensed by passing it through a condensation system, which the recycled water cooling system is the most commonly used method at present.
The crude oil product that you obtain from the pyrolysis process can be used as furnace oil but it isn't sufficiently pure for engines. If you want to use it as engine fuel, you need to extract and purify the desired products from the crude oil through a fractional distillation process.
And below are the normal distillation process by waste plastic to diesel plant:
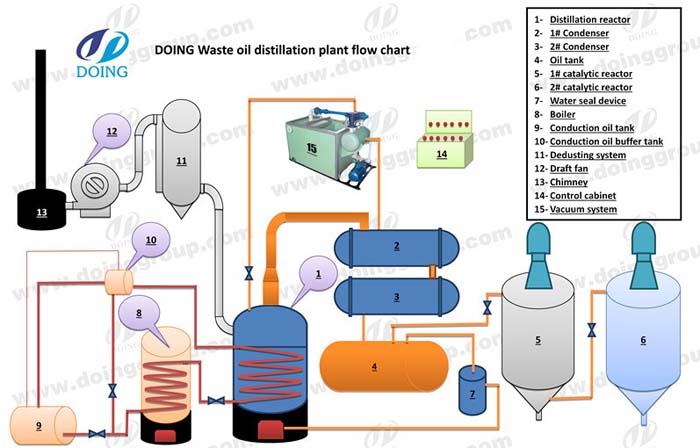
Working process of waste plastic to diesel plant
1.Pump the plastic oil to the distillation reactor
2.Heating
3.Condensation
4.Chemical processing
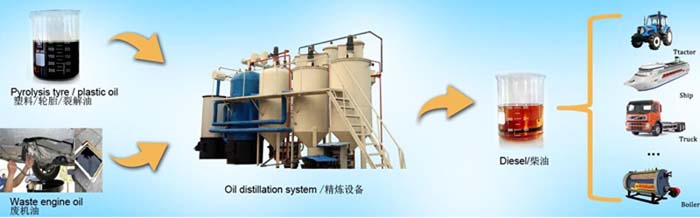
Waste plastic to diesel plant
Some benefits of pyrolysis and distillation are that the processes does not generate harmful pollutants and that the by-products can be used as fuel for running the plant. In the case of plastic, some of the valuable fuels and solvents that can be extracted through waste plastic pyrolysis are gasoline, kerosene, diesel, benzene, toluene and xylene. And a kilo of waste (typically PP) can yield upto a litre of fuel whereas the incineration of the same quantity of plastic would produce 3 kilos of CO2!
So through this process of pyrolysis and distillation, the bane of abhorrent plastic waste, can now become a boon and a source of abundant fuel. This will reduce plastic in landfills, reduce emissions and be a reliable alternative to the depleting fossil fuels. Don't trash your future. Act now!
Despite its amazing properties of strength, durability and its light weight, plastics have a major drawback: they can take up to 500-1000 years to naturally degrade. So if plastic had been discovered 500 years ago, and if Shakespeare used to brush his teeth, then his toothbrush would still be lying somewhere in someplace!
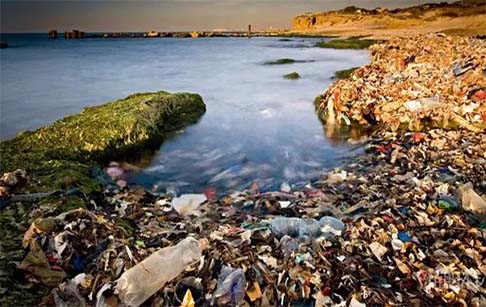
Waste oil
So what do we do with these ever-growing mounds of plastic waste? Bury plastic underground? Burn it? Or launch it into space! These solutions are more disastrous than the problem itself.
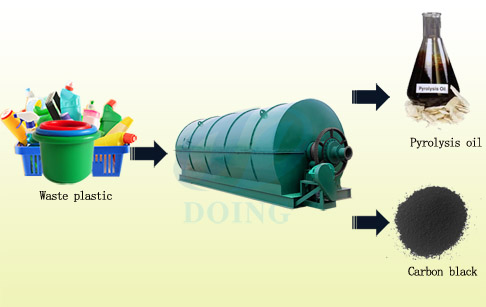
The basic pyrolysis process goes as follows:
1. Shredding or compressing for better feeding
Firstly, the waste material must be segregated and, if possible, be cleaned. Then it is shredded to speed up the reaction and to ensure that the reaction is complete.
2. Anaerobic heating
The shredded material must be heated in a controlled manner in an oxygen-free reactor. One of the most crucial factors in this operation is maintaining the right temperature(~430C for plastic) and the rate of heating, as they define the quality and the quantity of the final product.
3. Condensation
The gas that comes out from the reactor must be condensed by passing it through a condensation system, which the recycled water cooling system is the most commonly used method at present.
The crude oil product that you obtain from the pyrolysis process can be used as furnace oil but it isn't sufficiently pure for engines. If you want to use it as engine fuel, you need to extract and purify the desired products from the crude oil through a fractional distillation process.
And below are the normal distillation process by waste plastic to diesel plant:
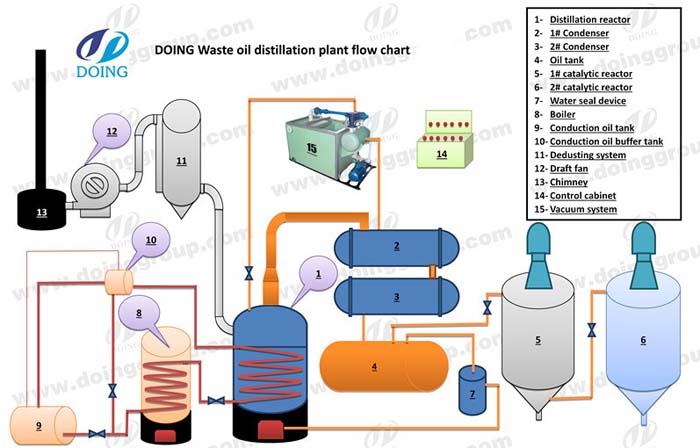
Working process of waste plastic to diesel plant
2.Heating
3.Condensation
4.Chemical processing
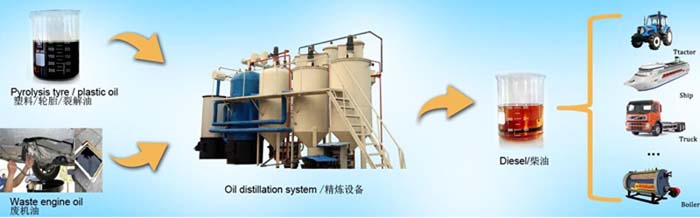
Waste plastic to diesel plant
So through this process of pyrolysis and distillation, the bane of abhorrent plastic waste, can now become a boon and a source of abundant fuel. This will reduce plastic in landfills, reduce emissions and be a reliable alternative to the depleting fossil fuels. Don't trash your future. Act now!
