Product
Project Case
-
DOING 15 TPD semi-continuous tire pyrolysis equipment installed in Indonesia
-
DOING 15TPD semi-continuous pyrolysis plant was installed in Brazil
-
1TPD Waste Oil to Diesel Refinery Machine Operation Site in Thailand
-
Transforming Paper Mill Plastic Waste into Diesel Plant Installed in Mexico
-
-
-
DOING Waste tyre to diesel recycling plants were successfully installed in Japan
-
Waste tire to diesel recycling plant was put into operation in South Africa
-
14MTPD Capacity of Waste oil recycling refinery plant project in Ghana
-
Continuous rubber tyre pyrolysis machine installed in Liaoning,China
FAQ
-
Continuous Pyrolysis plant
-
Oil Refining Machine
-
Auxiliary Equipment
Difference between continuous pyrolysis plant and batch pyrolysis plant
What are the differences between intermittent and continuous devices? This article mainly summarizes the similarities an...
-
Cell/WhatsApp: +86-135-2669-2320
-
Phone: +86-371-56771821
-
E-mail: market@doingmachinery.com
- Features:
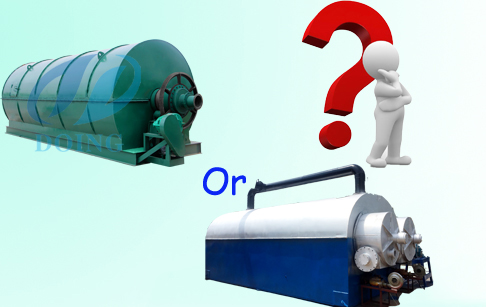
Continuous and batch type pyrolysis plant
The same points are mainly reflected in the following aspects:
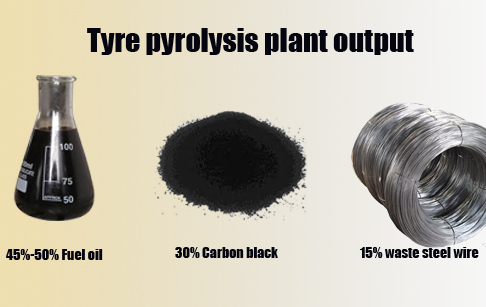
Both continuous and batch pyrolysis plant final products
1. The working principle of the two equipments is the same. All of them use high-temperature cracking chemical reactions. Through the heating of the reactor, the waste plastics/waste tires are subjected to pyrolysis chemical reactions.
2. The operation of two devices can eventually get fuel, carbon black, steel wire, combustible gas.
The differences are mainly reflected in the following aspects:
Intermittent equipment: After processing a batch of materials, it is necessary to pause for a period of time before the second material treatment is performed. After the reactor is cooled to a certain temperature, the next batch of materials is processed.
Continuous equipment: It can work continuously for 24 hours, continuous feeding on one side, continuous slag discharge on the other side, without pause cooling in the middle.
Required workers:
Intermittent equipment: Requires 3-4 people to maintain the normal operation of the equipment.
Continuous equipment: PLC control system, high degree of automation, saving manpower.
Feeding:
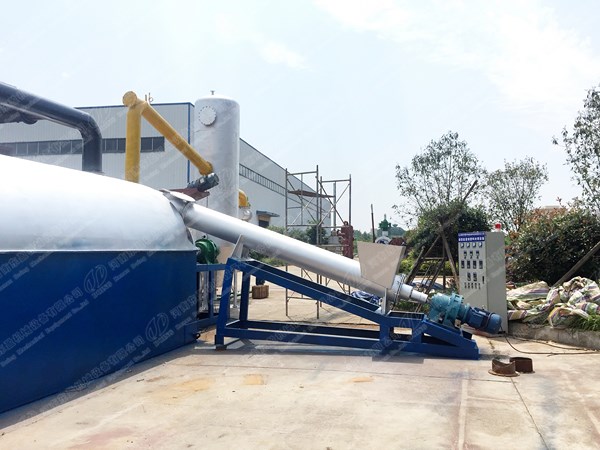
For continuous equipment, raw materials need to be broken in advance, and then feed through the screw device.
Slagging:
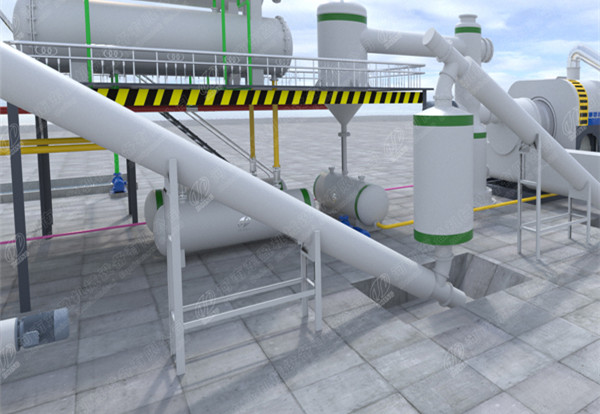
Intermittent equipment: Sealed slag discharge channels underground to ensure that the discharged carbon black does not fly around and pollute the air.
Continuity equipment: Carbon black is automatically discharged in a sealed environment through a screw conveyor.
Smoke removal method:
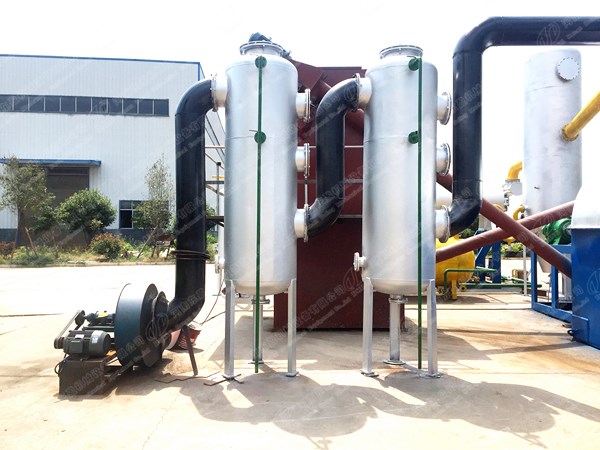
Intermittent equipment: three-layer high-pressure spray nozzles are used to remove small solid particles from the smoke. Or use a pulse dedusting device when the amount of smoke is large.
Continuity equipment: It is equipped with desulfurization and denitrification equipment, and the flue gas is purified and recycled. Some of the hot smoke that cannot be recovered is recycled into the reactor heating furnace for the purpose of supporting the heat.
Both devices have their own advantages. The main purpose is to allow you to have a deeper understanding of the two devices through this article, so as to choose the right one according to your own needs and the capital budget !!
Previous: Tire pyrolysis process
Leave A Message
Please feel free to leave your contacts here and your privacy is protected. A competitive quotation will be provided according to your detailed requirement within one business day.
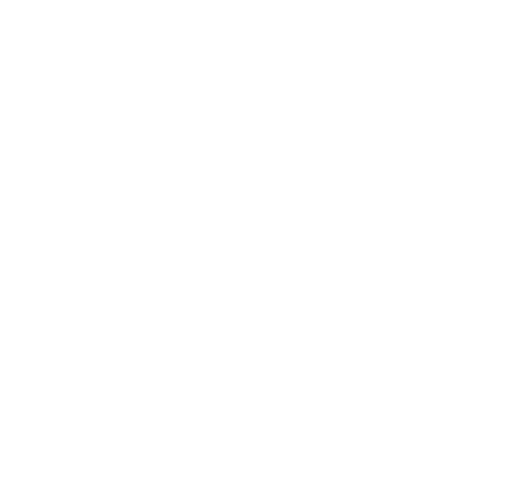